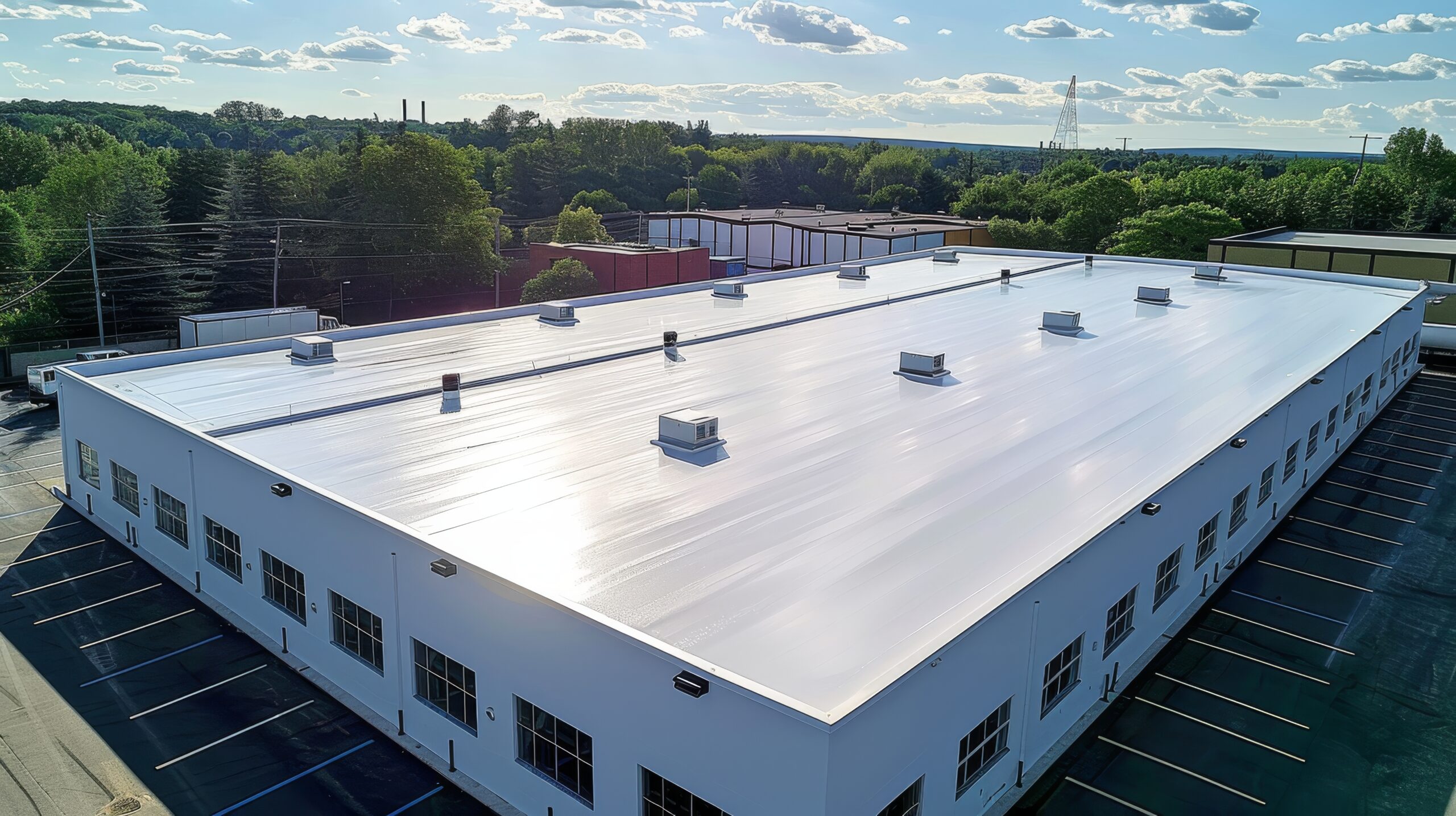
PVC (Polyvinyl Chloride) roofing systems have been widely embraced by commercial, industrial, and institutional buildings for six decades. Their popularity stems from their longevity, ability to withstand severe weather, and cost-effective installation and repair.